Quality Steel Solutions
From iron ore to core (ferrite-pearlite) TMT steel rebar, we deliver excellence in every product we offer.
Product Range
High-quality steel products with state-of-the-art technology and strict quality control at AISCO
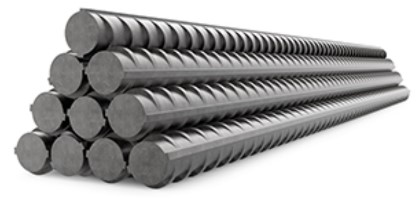
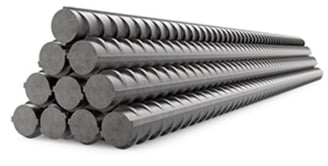
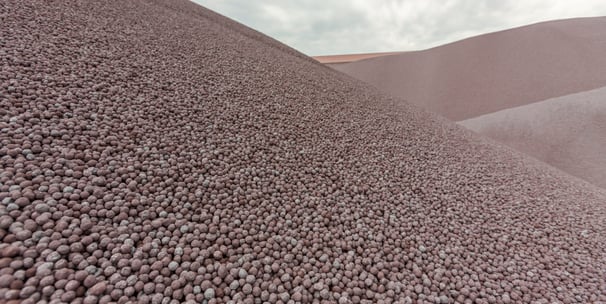
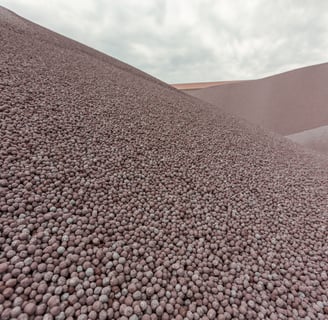
Iron Ore
Transforming iron ore into premium steel products
TMT Steel
Greater Strength and Guaranteed Ductility
AISCO TMT Rebars are produced using its basic concept of Ore to Core, where sponge iron, billets, and TMT bars are manufactured in the integrated steel plant under strict monitoring and control of AISCO, ensuring total quality control during the production process like other main producers. AISCO TMT bars are produced in selected state-of-the-art manufacturing units, using direct reduced iron (DRI) for the production of quality castings. Sponge iron with inherent characteristics like virgin nature, low sulphur and phosphorous contents, and consistent composition, procured with good strength and high metallic contents, melts in the furnace. Samples are drawn from each heat from the beginning, middle, and end of the heat. Chemicals are controlled by ladle analysis, and alloys are added as per the desired chemical composition. The molten steel is tapped into a ladle and taken to the Continuous Casting Billet Machine (CCBM) to be cast into billets, and these billets are then rolled into TMT bars through an automatic rolling mill with an international quenching technology process for a ferrite-pearlite core.
Raw Material (Iron Ore)
Strive to attain top quality in the ultimate product, starting right from the stage of procuring raw materials for sponge iron, i.e., iron ore, non-coking coal, and dolomite. The quality of sponge iron is highly sensitive to the characteristics of the raw material. Therefore, it is essential to examine the chemical and physical characteristics of raw materials, both individually and in combination, and hence strict quality checks are applied while procuring raw materials at this stage. Iron ore with high Fe content and low gangue content is only preferred to optimise yield during steelmaking. The iron ore is also made to undergo a series of other tests like shatter, tumbler & abrasion indices, reducibility, etc. To attain desired results, the raw materials are sourced only from the top-quality mines.
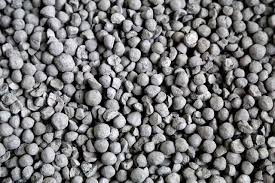
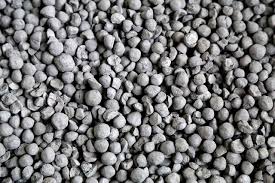
Sponge Iron
Special care is taken to ensure the following qualities in the sponge iron produced:
(a) Low sulphur and low phosphorus
(b) Uniform quality
(c) High iron content and high degree of metallisation
(d) Minimum dust generation
(e) Negligible tramp element and low gangue contents
Sponge Iron
Uniform-quality sponge iron for steel production.
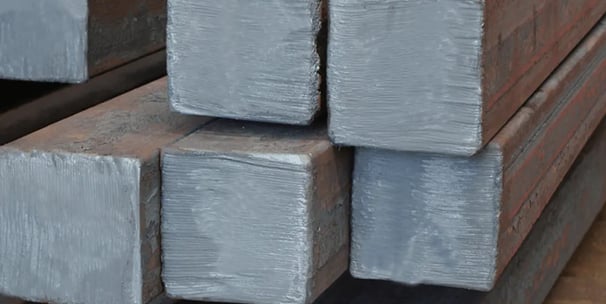
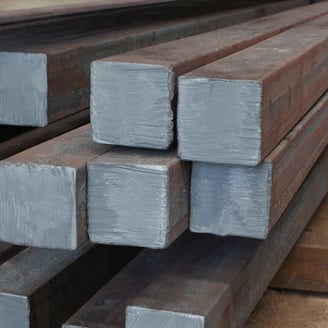
Billets
High-quality billets for TMT rebar process
Casting of Billets
Internally produced, high-quality sponge iron is then cast to manufacture billets at a fully integrated mill. Strict quality checks at every stage ensure the required chemical mix for every charge. Samples are checked for every heat manufactured for chemical compositions. Steel billets are rolled through a sequence of rolling stands, progressively reducing billets to the desired size. From here, the three-stage process of “quenching and tempering” starts.
Thermomechanical Treatment Process for Reinforcement Bars
The use of the thermomechanical treatment process has not only helped produce rebars of high yield strength but also has superior ductility, weldability, bendability, better corrosion resistance, and thermal resistance, creating a revolution in reinforcement engineering. AISCO’s high-quality reinforcement bars are produced at the most advanced, fully automatic, high-speed rolling mill through the “Quenching and Tempering Process” with international technology.
Quenching is the first stage where, after leaving the final roll, the bar enters the fully automatic and computerised quenching box to undergo the quenching, where water is sprayed on the surface of the rebar to bring down the temperature of the surface of the bar to the desired temperature. It hardens the outer surface called “martensite.”. The core here remains austenitic.
Self-tempering is the next stage. The bar leaves the quenching box with the temperature of the core being higher than that of the surface. This allows heat to flow from the core of the surface, resulting in the tempering of the surface. This gives a strong and tough outer surface called “tempered martensite." The core remains austenitic at this stage.
Atmospheric cooling is the final stage; cooling of rebar takes place when it reaches the walking cooling bed (automatic mechanised), finally turning the austenitic core into a ferrite-pearlite core, which is ductile. The process of “quenching and tempering” thus results in an outer rim at the surface that is tough and strong and a ductile centre, giving the rebar a combination of strength and ductility. The mechanised cooling bed ensures proper cooling of every single piece of TMT bar from all sides of the surface. This makes it possible to form a uniform circular rim throughout the length of the bar, definitely giving an edge over the other TMT bars, which are cooled at ordinary beds.
AISCO TMT: A Zero-Defect Quality Product
The AISCO team follows the basic philosophy of “Quality Begins with Me." The quality checks begin right from the stage of procurement of raw materials like iron ore and coal, dolomite, and other various minerals and alloys, etc., and are followed till the final product is received.
AISCO’s infrastructure is fully equipped to ensure quality checks at every stage. AISCO has a well-equipped laboratory for all kinds of quality tests, including the latest spectrometer for the most accurate chemical analysis, and the following tests are regularly conducted to ensure the desired quality:
Ladle Analysis Chemical Analysis
Tensile Test
Bend/Re-bend Test
The ultimate aim is to provide a zero-defect quality product to the consumers and to set standards for the steel industry in terms of quality.
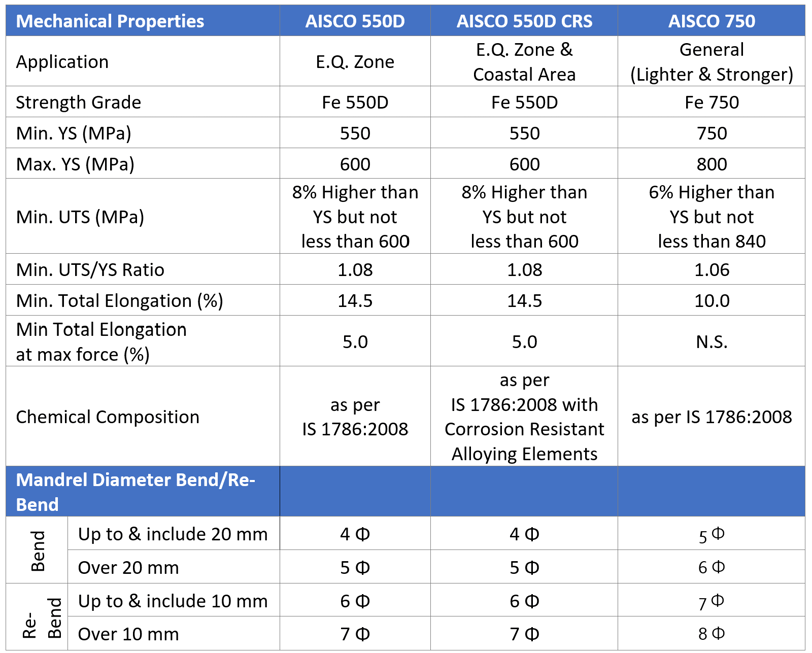
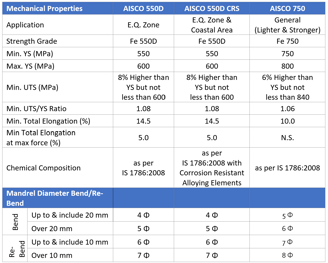
High Strength Deformed Steel Bars for Concrete Reinforcement as per IS 1786:2008
equivalent to international standards like ASTM A615 (USA), DIN-488:86 (Germany), and BS 444-2005 (Britain)
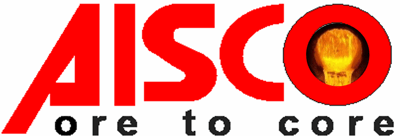
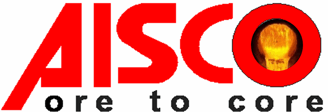
At Aisco, we specialise in high-strength TMT rebars, ensuring superior quality and compliance with IS 1786 standards, tested, inspected, and certified by the national BIS-recognised and the world’s leading international laboratories.
National Metallurgical Laboratory
Delhi Test House
Shriram Institute for Industrial Research
National Test House
MSME Testing Centre
Bureau Veritas Consumer Products (India) Pvt. Ltd.
SGS India Private Limited
Spectro Analytical Labs Private Limited
TUV SUD South Asia Pvt. Ltd.
Quality Steel Reinforcement Solutions
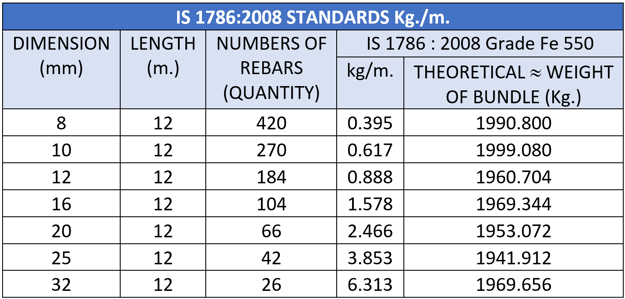
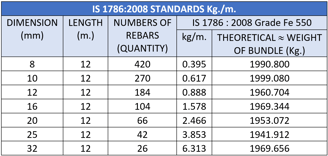